
About Cast Metals
Large cast metal pieces are unusual within the hobby. I've put together this page further explaining the process for casting metals! I'll be going into detail on the cast iron process in particular, but this is fairly similar to that of cast bronze as well.
The Casting Process
Some aspects of the casting process are actually very similar to those of cast resin models, but with far more steps involved. I cast this Breyer Clydesdale in iron as a test for my Breyerfest 2021 Best Customs Contest entry. I acknowledge that no one should be molding and casting ANY Breyer model, however cast iron is very brittle and thinner parts of a casting are subject to break during de-molding the metal casting. Almost any model horse scaled sculpture would be destroyed if cast in iron using the following methods. This is the reason I had to cast this "test piece" before committing to casting my entry for the contest.
The casting process for this test piece starts at making a rubber mold of the piece so a wax casting can be obtained. A brush-on rubber mold is a more economical way to create a mold as less rubber is used in the mold making process. The downside to this mold requiring a rigid plaster mold that supports the rubber known as a "mother mold". Once the mold is created, a wax copy can be cast and cleaned. Wax feeders called a sprue system are attached to the casting. This leaves a pathway for the metal to flow and a ventilation system for air to escape to prevent entrapment. The wax casting is then dipped into a secondary mold making material called ceramic shell. After being dipped in the slurry, the piece is coated in multiple layers of fine sand to create a shell around the wax.
Once the shell is thick enough, it is placed into a kiln at a temperature that melts the wax from the shell, creating a hollow cavity for the metal to be poured into. After all the wax is gone, the temperature is risen to vitrify the shell. The kiln is then turned off, and shells are removed once cool to check for cracks and breaks. Any issues are patched, and the shell is placed in an insulated bin and heated once again.
While the shells are heating up, so is the furnace! Iron casting is a team effort and takes a lot of setting up! Once the furnace has been lit and fed charges of both iron and refined coal, a crew is dedicated to keeping her happy. When enough iron collects at the bottom of the furnace, a pour team is called with a ladle to position themselves at the front of the furnace. A plug of "mud" is tapped through, allowing metal to flow through the tap hole and into the ladle. This can be anywhere from 100 to 150lbs of molten iron. After the metal is out, it is re-plugged and the process is repeated. Impurities float to the top of the metal and are skimmed off before the ladle is walked around to pour as many molds as possible. After all the molds are poured and the furnace is taken care of we celebrate a job well done, clean up the next day, and de-mold our castings!
The de-molding process is where things get tricky for those thin legs. The shell must be chiseled away. Cast iron is very brittle, and any thin legs would shatter. Even this chunky Clydesdale wasn't spared. Once all the shell is removed the sprue system is no longer needed and gets cut away. Scars from the sprues must be ground away using a variety of air and power tools until it is invisible. Any bubbles and casting defects are fixed up.
Once the casting is prepped, it is time for patina! Patinas are a layer of oxidation on the metal's surface. We can achieve what would take 100's of years in some instances in hours to minuets with heat and a variety of acids. Iron only wants to rust, but bronze has a wide array of colors that can be applied! After a good cleaning, the piece is heated. Each chemical is applied at a different temperature. If that temperature is wrong, the wrong color will form. I can only touch the surface of the metal to gage if it is ready for chemical. If it is hot enough, chemical is brushed, sprayed, or layered depending on the end goal. Many different techniques such as burnishing and dark undercoats are applied to achieve different effects. Once the right color forms, it is sealed in a coat of wax to protect the patina.
Then you are ready to enjoy your finished casting! All metal casting is a labor of love, but nothing can compare to the end result. Iron in particular is a material that can present challenges, but it has given me amazing experiences, a place to belong, and the community I call my family.

Prepped for mold making

Wax casting pulled from the mold
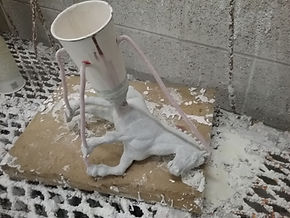
The wax casting and it's sprue system after the first sand coating
Massachusetts College Of Art and Design's Iron Corps competing in the 2023 National Conference On Contemporary Cast Iron Art and Practice's Student Cupola competition at Sloss Furnaces in Birmingham Alabama. Photos credited to the Massart Iron Corps

A broken leg!

Removing scars from the sprues

Cold patina chemical application

Metal is heated to the correct temperature

Best Customs Contest entry 2021. He was featured on Breyer's site if anyone remembers him!